Epoxy vs. Traditional Barrier Coatings: What Makes Spin Cast Spray Application More Reliable?
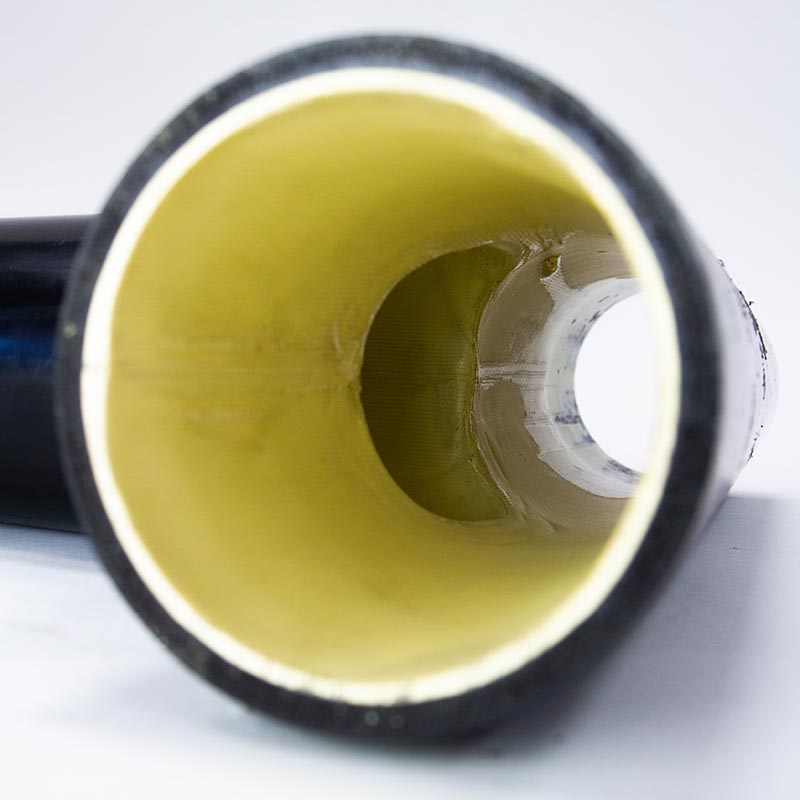
When it comes to protecting pipelines, plumbing components, and industrial infrastructure, choosing the right barrier coating is critical. While brush-on and dip coating methods have been widely used for decades, epoxy spin cast barrier spray coating has emerged as a superior solution—especially in high-wear or corrosive environments. This advanced technique ensures stronger protection, longer lifespan, and greater efficiency for both residential and commercial applications.
Precision and Consistency Matter
Traditional barrier coatings, such as brush-on or dip methods, can lead to uneven application. Brush-on coatings are subject to human error, which may result in thin spots, streaking, or inconsistent coverage. Dip coatings, while useful for small or symmetrical parts, can create uneven buildup in tight areas and fail to penetrate complex internal surfaces effectively.
In contrast, epoxy spin cast barrier spray coating delivers a uniform, 360-degree application by combining centrifugal force with high-performance epoxy resins. The component is rotated at high speed while the epoxy is sprayed, ensuring the coating is applied evenly across every surface—even inside narrow bends or hard-to-reach areas in pipes. This consistent coverage helps eliminate weak spots that often lead to premature failures in traditional coatings.
Superior Abrasive and Corrosion Resistance
One of the main advantages of epoxy spin cast barrier spray coating is its exceptional durability. Epoxy resins form a tough, chemical-resistant shell that stands up to abrasion, corrosion, and temperature fluctuations. In environments like water treatment facilities, chemical plants, or industrial plumbing systems—where high flow rates and corrosive substances are common—this method dramatically outperforms conventional coatings.
Brush-applied or dip-coated systems tend to wear out faster, especially at contact points or sharp angles. Over time, these exposed areas become susceptible to rust, leaks, or scaling, often requiring costly repairs or replacements. The enhanced bonding strength and surface penetration of spin cast epoxy mean longer-lasting protection and fewer maintenance issues.
Faster Application and Cure Times
Time is money in any industry, and epoxy spin cast barrier spray coating helps reduce both labor hours and downtime. Spin casting enables faster application over large areas, eliminating the tedious process of hand-brushing or repeated dipping. Moreover, epoxy formulas used in spray systems are often engineered for faster curing, allowing coated components to be returned to service more quickly.
This efficient process is especially beneficial for high-volume operations or emergency repairs—making it a smart choice for infrastructure managers and plumbing professionals alike.
The Smart Choice for Lasting Protection
If you’re looking for cutting-edge protection for your plumbing systems, Upstate South Carolina’s preferred plumber recommends considering the long-term value of epoxy spin cast barrier spray coating. Its unmatched consistency, durability, and efficiency make it the go-to solution for demanding environments where failure is not an option.
Call us at Mathis Plumbing & Heating Co., Inc. today to learn more about our epoxy spin cast barrier spray coating services in Upstate South Carolina. Let us help you extend the life of your systems with a solution that delivers reliability from the inside out.
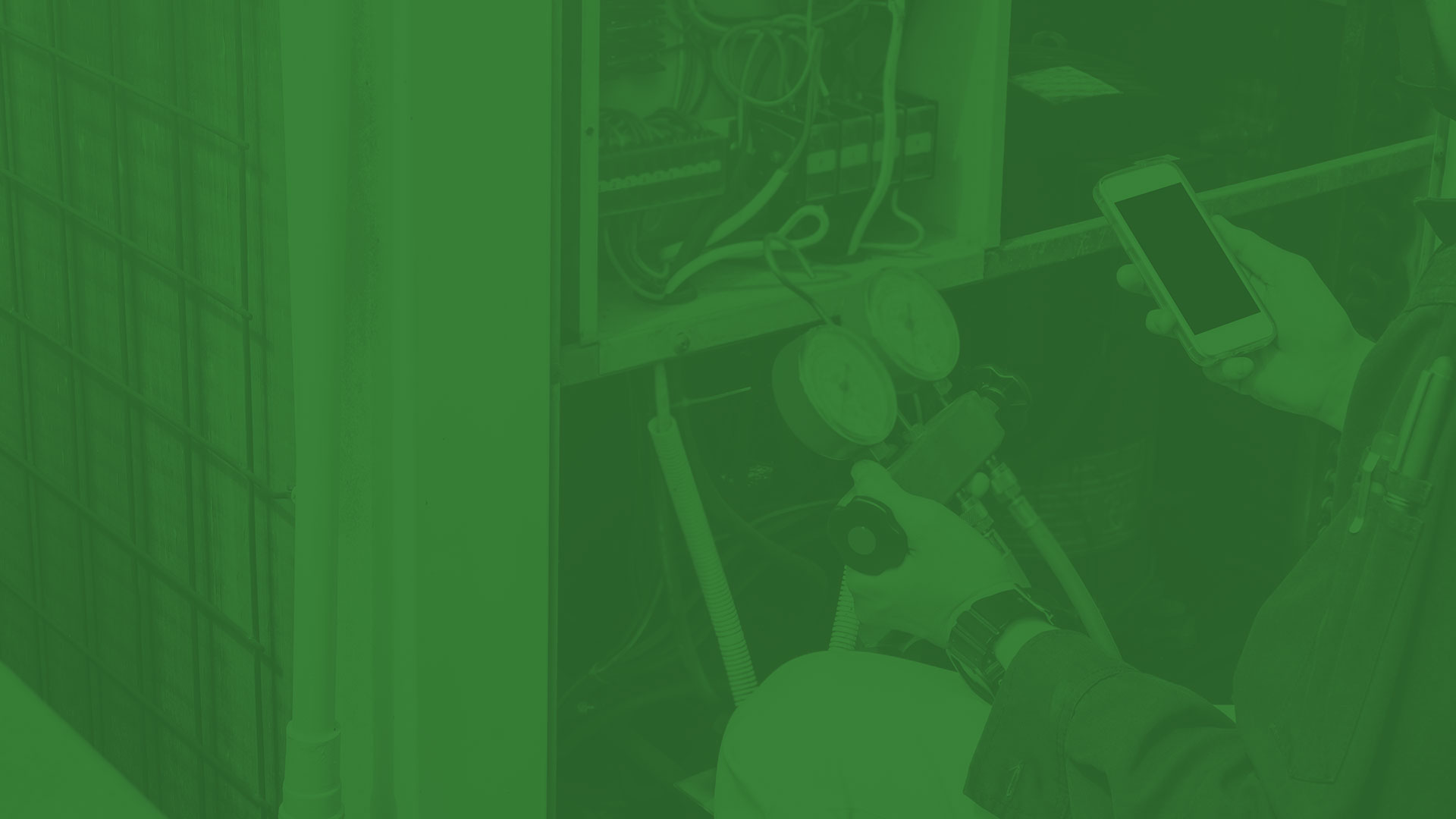